A reliable integrated system that realizes high quality and lower cost.
We develop all manufacturing processes under strict quality controls. |
 |
To provide high quality gears in a sort lead-time at lower cost,
we have always made every effort to establish an automated and integrated production
system for the complete production process. We will continue to improve our production
process to meet the more diversified and sophisticated needs of our customers. |
|
Typical manufacturing process for pinion gear |
 |
 |
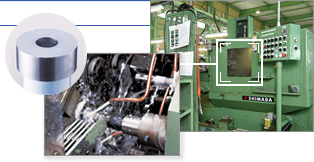 |
|
The most suitable material such as round bars or hot or cold
forging steel is selected according to the customer's requirements. We usually
use round bars cut into pieces for pinion gears. |
|
|
 |
 |
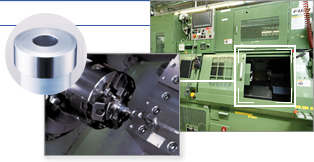 |
|
Rough and finish cuts are done in succession mainly by NC lathe
and other machining process such as drilling or broaching is added if neces-sary. |
|
|
 |
 |
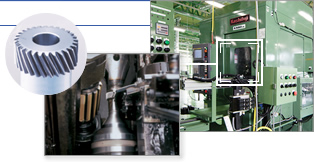 |
|
Various pinion gears are made by hobbing, shaper and rolling
machines before heat treat-ment. By using a special hobbing machine developed
by Nakamura we can cut high helical gears easily and speedily. |
|
|
 |
 |
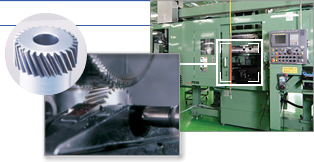 |
|
The tooth surface of a pinion gear is finished by gear shaving
or using a rolling machine before heat treatment. The chamfering and trimming
processes are usual preceded by the finishing process. |
|
|
 |
|
 |
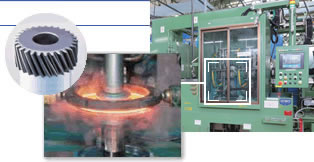 |
|
Surface hardening such as carburizing, nitriding and high-frequency
quenching is done to increase gear strength. Shot peening is added if needed. |
|
|
 |
 |
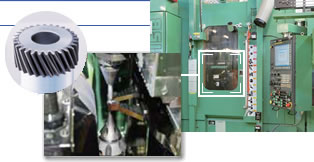 |
|
The roughness and accuracy of the gear is improved by external
and internal grinding and at the edge of the product. |
|
|
 |
 |
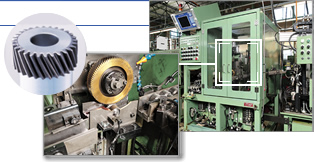 |
|
Burrs, dents and flaws of gears are inspected by special gearing
test machines. |
|
|
 |

|
Production controls on our lines are performed using Kanban and Andon methods.
Kanban is used to inform if there is a delay in the production process or if
it has advanced. Andon informs operators of the current status of the production
system. Kanban is divided into three types: Supplier Kanban, Intra-process Withdrawal
Kanban and Withdrawal Kanban.
"Kanban" is a sign to give instruction for production or conveyance
of items. "Andon" is an electric light board used as a visual control
device in a plant. |
 |
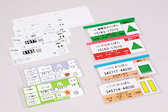 |
|
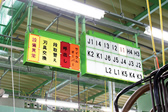 |
"Kanban" s used in us |
|
"Andon" in our plant |
 |
|
|
|